Business
Custom Fabrication for the Automotive Industry Challenges and Solutions
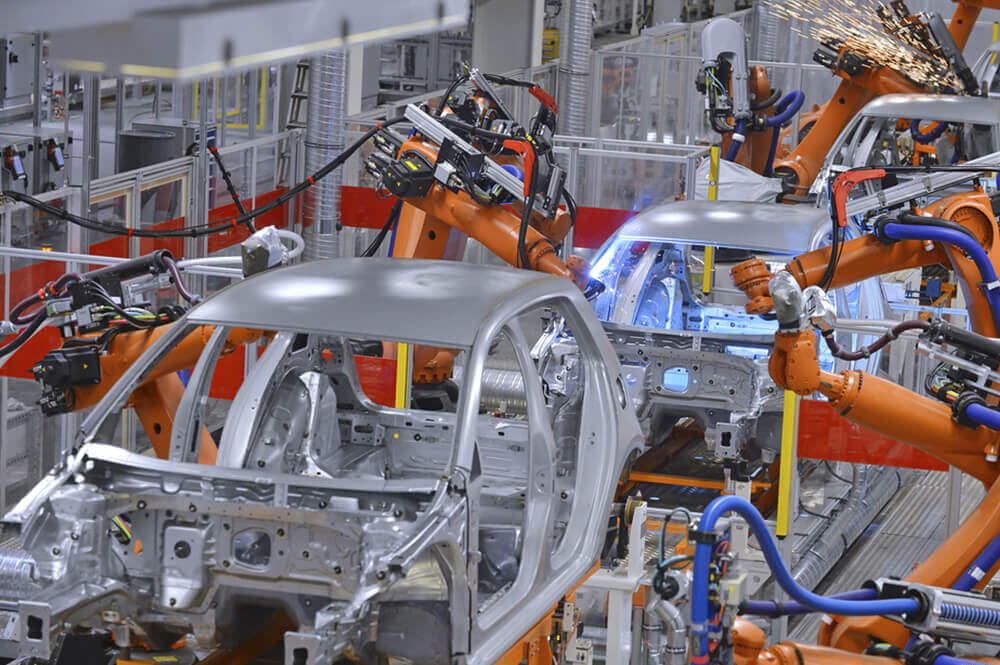
The automotive industry is in a state of constant evolution, driven by technological advancements and the demand for more efficient, reliable, and innovative vehicles. Custom fabrication plays a crucial role in meeting these demands, allowing for the creation of bespoke components tailored to specific applications. However, custom fabricators and CNC machining companies face a unique set of challenges in this dynamic sector. This blog explores these challenges and the solutions that enable successful custom fabrication for the automotive industry.
Meeting High Precision and Quality Standards
Precision and quality are paramount in automotive manufacturing, where even minor deviations can lead to significant issues. Custom fabricator companies must adhere to stringent standards to ensure that each part meets exact specifications. This challenge is particularly pronounced when dealing with complex geometries and tight tolerances required for automotive components.
To address this, CNC machining companies employ advanced machining technologies and rigorous quality control processes. Multi-axis CNC machines, for instance, allow for precise machining of intricate parts, while real-time monitoring systems ensure consistent quality throughout the production process. These measures help custom fabricators maintain the high standards necessary for automotive applications.
Managing Material Selection and Utilization
The choice of materials is a critical factor in custom fabrication for the automotive industry. Components must be lightweight yet strong, durable, and capable of withstanding harsh conditions. Common materials include aluminum alloys, high-strength steels, and advanced composites. However, selecting the right material involves balancing performance, cost, and manufacturability.
Custom fabricator companies rely on their expertise and advanced material science to choose the optimal materials for each application. CNC machining companies also use simulation and modeling tools to predict material behavior and optimize the machining process. This approach ensures that the final products meet the required performance criteria while minimizing waste and reducing costs.
Ensuring Consistency and Repeatability
Automotive manufacturers demand high-volume production with consistent quality across all parts. Achieving this level of consistency and repeatability is a significant challenge for custom fabricators. Variability in the manufacturing process can lead to defects and deviations, impacting the overall performance and reliability of the vehicle.
CNC machining companies tackle this challenge by implementing standardized operating procedures and leveraging automation. Automated CNC machines can operate with minimal human intervention, reducing the risk of errors and ensuring uniformity in production. Additionally, statistical process control (SPC) techniques are employed to monitor and control the manufacturing process, ensuring that each part meets the desired specifications.
Adapting to Rapid Technological Advancements
The automotive industry is characterized by rapid technological advancements, from electric vehicles to autonomous driving systems. Custom fabricator companies must stay ahead of these trends and adapt their processes to meet the evolving demands. This requires continuous investment in new technologies and ongoing skill development for their workforce.
CNC machining companies address this by incorporating the latest advancements in machining technologies, such as additive manufacturing and advanced robotics. By integrating these technologies, custom fabricators can enhance their capabilities, reduce production times, and increase flexibility in handling new and complex projects. Additionally, ongoing training programs ensure that employees are equipped with the knowledge and skills needed to work with cutting-edge technologies.
Managing Supply Chain and Logistics
Efficient supply chain and logistics management are crucial for timely delivery and cost-effective production in the automotive industry. Custom fabricator companies often face challenges related to sourcing high-quality materials, managing inventory, and coordinating with multiple suppliers. Disruptions in the supply chain can lead to delays and increased costs, affecting the overall efficiency of the manufacturing process.
CNC machining companies mitigate these challenges by establishing strong relationships with reliable suppliers and implementing robust supply chain management strategies. Just-in-time (JIT) inventory systems, for example, help reduce inventory costs and ensure that materials are available when needed. Additionally, advanced planning and scheduling software enable custom fabricators to optimize production schedules and improve coordination with suppliers.
Addressing Environmental and Regulatory Requirements
Environmental sustainability and regulatory compliance are critical considerations in the automotive industry. Custom fabricator companies must ensure that their manufacturing processes adhere to environmental regulations and minimize their ecological footprint. This includes managing waste, reducing emissions, and using eco-friendly materials.
CNC machining companies implement various strategies to address these requirements. Energy-efficient machining practices, recycling programs, and the use of sustainable materials are some of the measures taken to minimize environmental impact. Custom fabricators also stay informed about changing regulations and industry standards, ensuring that their operations remain compliant and sustainable.
Enhancing Collaboration and Communication
Effective collaboration and communication are essential for the success of custom fabrication projects in the automotive industry. Custom fabricator companies must work closely with automotive manufacturers, designers, and engineers to understand their requirements and deliver tailored solutions. Miscommunication or lack of collaboration can lead to delays, rework, and suboptimal outcomes.
CNC machining companies foster collaboration through digital platforms and integrated software solutions. Computer-aided design (CAD) and computer-aided manufacturing (CAM) tools facilitate seamless communication and coordination between different stakeholders. Virtual prototyping and simulation enable custom fabricators to validate designs and make necessary adjustments before production begins, ensuring that the final product meets the client’s expectations.
Leveraging Data and Analytics
Data and analytics play a vital role in optimizing custom fabrication processes and improving decision-making. CNC machining companies collect and analyze data from various stages of the manufacturing process to identify trends, monitor performance, and predict potential issues. This data-driven approach enables custom fabricators to make informed decisions and continuously improve their operations.
Custom fabricator companies use advanced analytics tools to track key performance indicators (KPIs), such as production efficiency, defect rates, and lead times. By analyzing this data, they can identify areas for improvement and implement corrective actions to enhance overall productivity and quality. Predictive maintenance, powered by data analytics, also helps minimize downtime and extend the lifespan of machining equipment.
Custom fabrication for the automotive industry presents numerous challenges, from meeting high precision standards to managing supply chains and ensuring regulatory compliance. However, by leveraging advanced CNC machining technologies, implementing robust quality control processes, and fostering collaboration, CNC machining companies and custom fabricators can overcome these challenges and deliver high-quality, bespoke components that drive innovation in the automotive sector. As the industry continues to evolve, these solutions will play a crucial role in shaping the future of automotive manufacturing.
-
Education1 year ago
What is TTU Blackboard: Everything You Need to Know
-
Health1 year ago
Ztec100.Com Tech Health And Insurance
-
Business1 year ago
Unlock the Power of an Online Survey Maker – A Comprehensive Guide
-
Game1 year ago
How to Use Try Hard Guides Wordle Solver Tool?
-
Tech1 year ago
A Comprehensive Guide: CRYPTONEWZHUB.COM COMPUTER
-
Tech1 year ago
Trendzguruji.Me Awareness: Digital Landscape Of 2024
-
Travel1 year ago
Fly And Swap Vacations Tips And Tricks You Need To Know
-
Entertainment1 year ago
Everything about 588 Area Code